
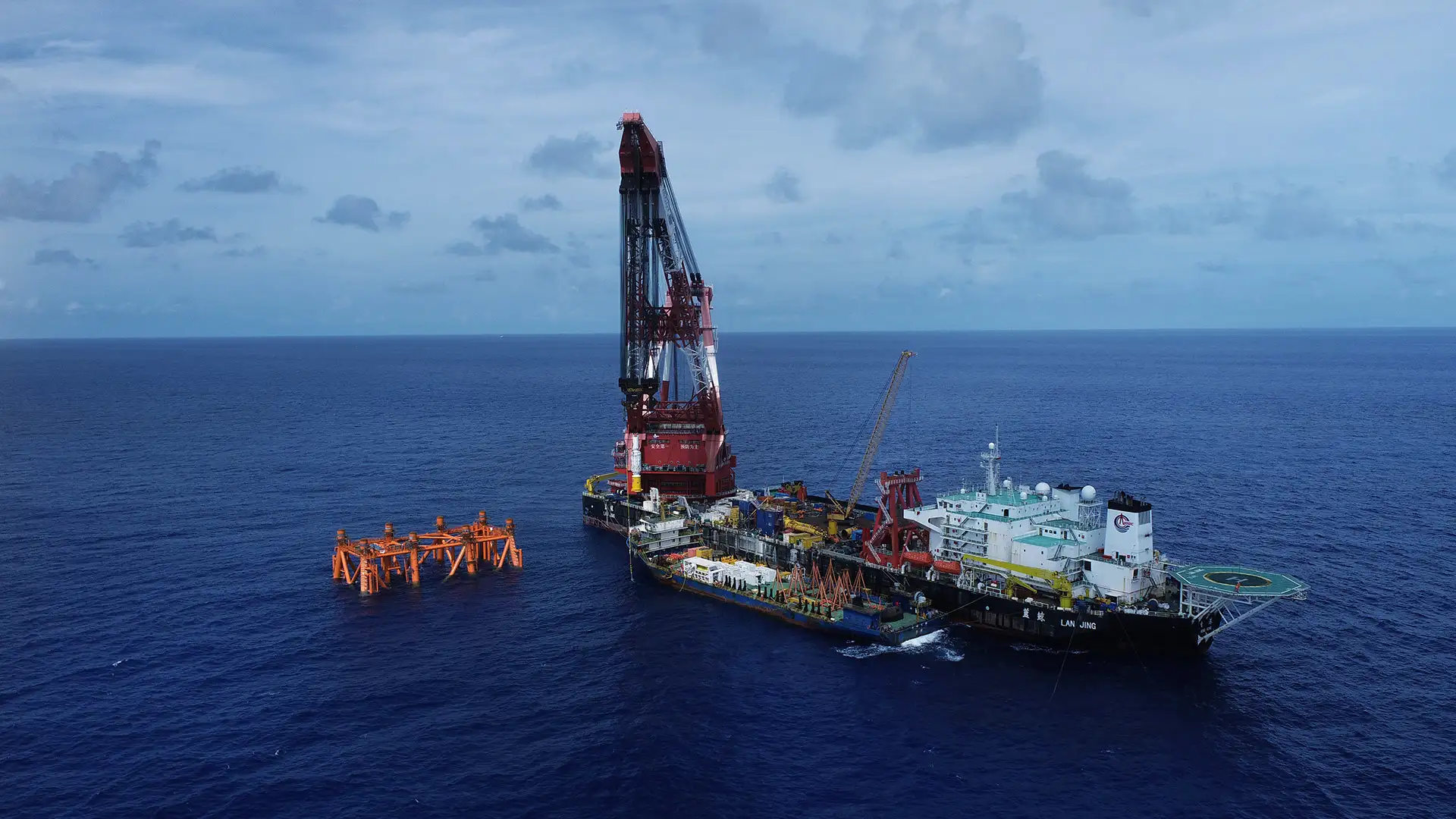

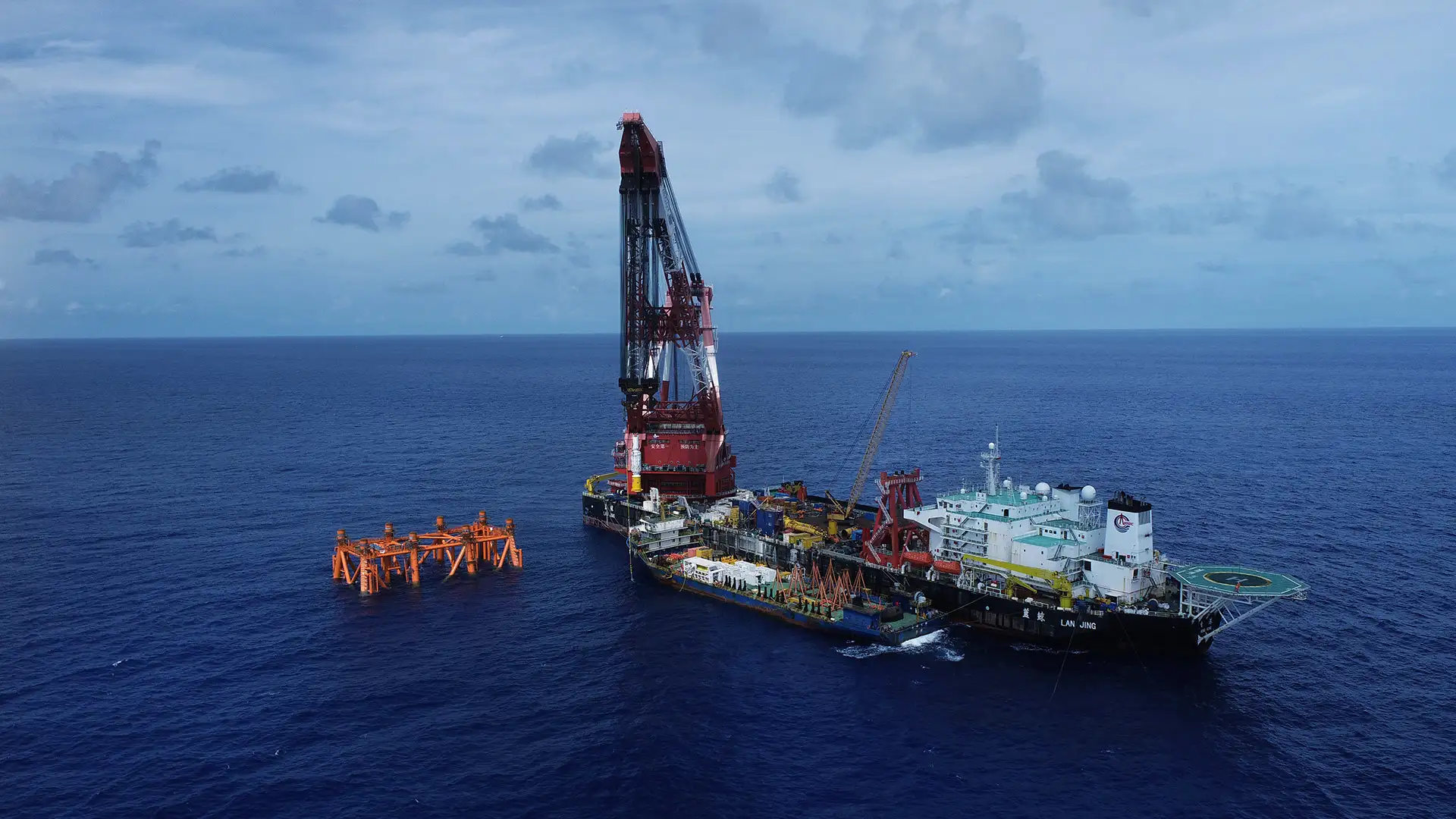
News
CFM News
The Construction of the State Power Investment Xuwen Capacity Increasing Project successfully Completed
CFM participated in the construction of the Xuwen Capacity Enhancement Offshore Wind Farm Project undertaken by the Guangzhou Salvage Bureau, which was the successful completed.
2024-10-16
Accelerate the development of new quality productivity · front-line research|"Nail" more than 100-meter-long steel piles into the 2,500-meter deep seabed, Nantong makes "super hammer" to make the offshore platform "stand"
Committed to the development of high-end marine equipment, CFM successfully developed China's first 2500 kJ large hydraulic piling hammer in 2018, which was officially installed at the end of 2019. In 2021, the first domestically produced YC-3500 kJ double-acting fully hydraulic piling hammer was delivered to the Guangzhou Salvage Bureau Huatianlong Ship Equipment for use, and nearly 100 steel piles have been laid in the South China Sea so far.
2024-05-01
Global Layout
CFM will insist on the developing strategy of “controlling key, mastering core, basing on high-end and facing international”, and adhering to philosophies “adoring craftsman, to be diligent and pragmatic, pursuing excellence, to become pioneers”. CFM will do the best to build the state-level and international competitive industrial base for green intelligent forging and piling machinery.
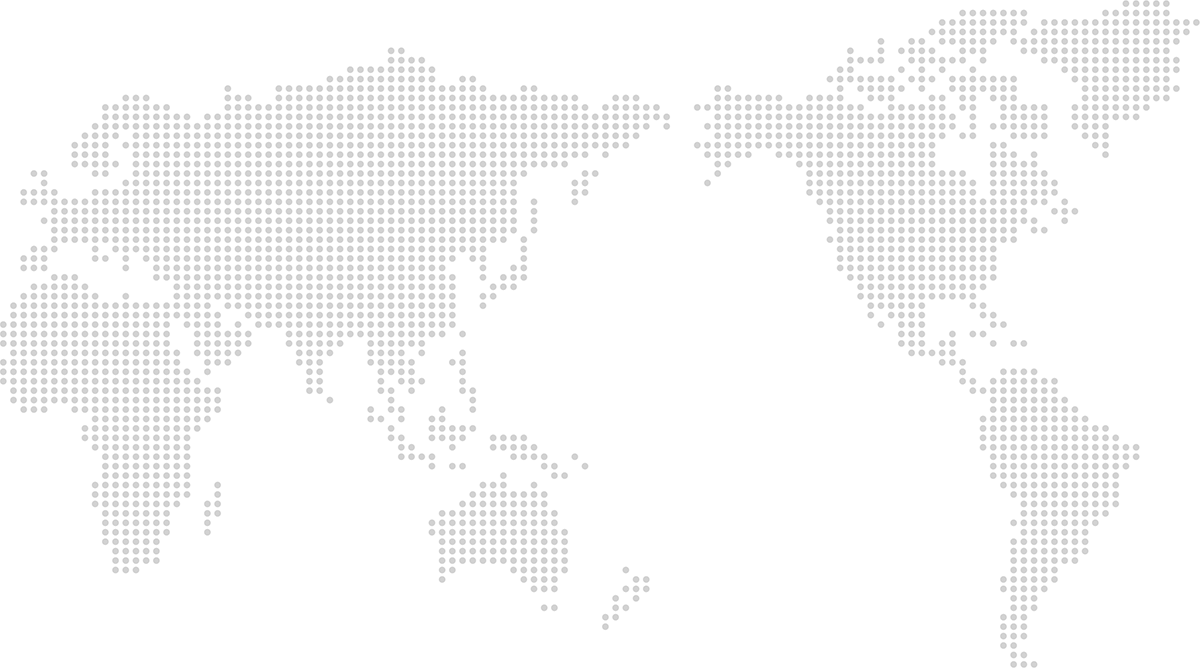